- 09 April 2021
- Door Bart Denys
INNOVATIVE PHOTOREACTOR OFFERS GROWTH OPPORTUNITIES FOR FLOW CHEMISTRY
costaTM TECHNOLOGY IN hanuTM FLOW REACTOR FACILITATES
INDUSTRIAL UPSCALING
As a subsidiary of Ecosynth, Creaflow moved into the brand-new building of BlueChem, the sustainable chemistry incubator that supports start-ups and scale-ups as part of their growth trajectory, early in the year 2020. Creaflow's development of its innovative photochemical HANUTM flow reactor opens up the possibility of producing new molecules on a larger scale, to overcome the limitations of conventional photoreactors. Koen Van Aken (CEO) and Hannes Gemoets (Head of R&D) rhapsodize about their innovation, while looking ahead to its successful worldwide marketing.
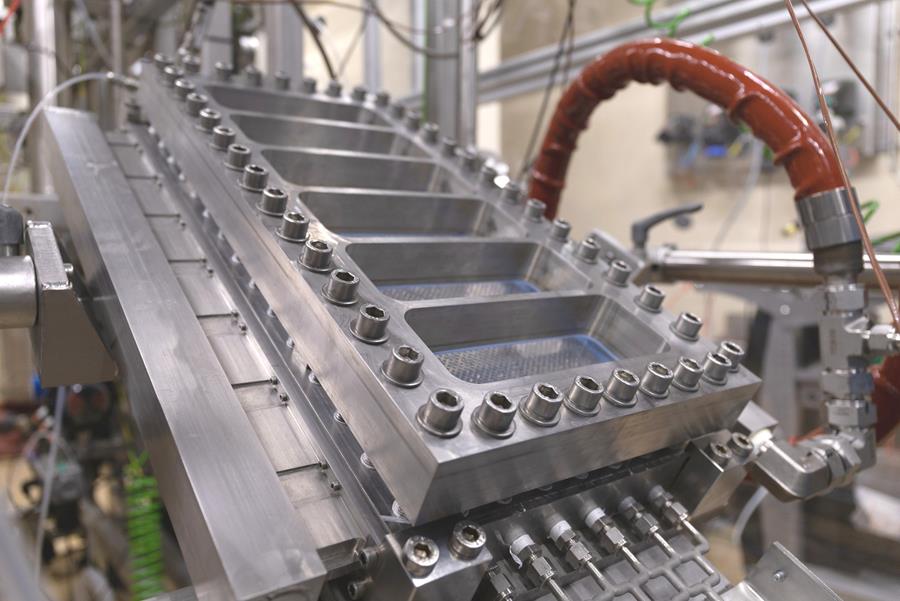
SUSTAINABILITY TRAILBLAZER
Creaflow was launched in 2018 as a spin-off of Ecosynth, which itself was founded in 2001 for the purpose of lending support to the chemical and pharmaceutical industries in their transition to sustainable chemistry.
Koen Van Aken, The CEO of Ecosynth and Creaflow takes a look back at what has been achieved to date: "Sustainability was still in its infancy back in 2001. Right from the very start, we consciously opted for a hybrid business model, so that we would perform contract research for third parties while undertaking our own R&D projects. Our research efforts have concentrated on both developing new molecules and creating more innovative and efficient processes. The focus under this heading was on niche areas where we could build up specific areas of expertise, in order to exploit these later on, through licensing our own patents and spin-offs, for example.
Photochemistry is a niche market that was confined for a long time to laboratory settings in the research community
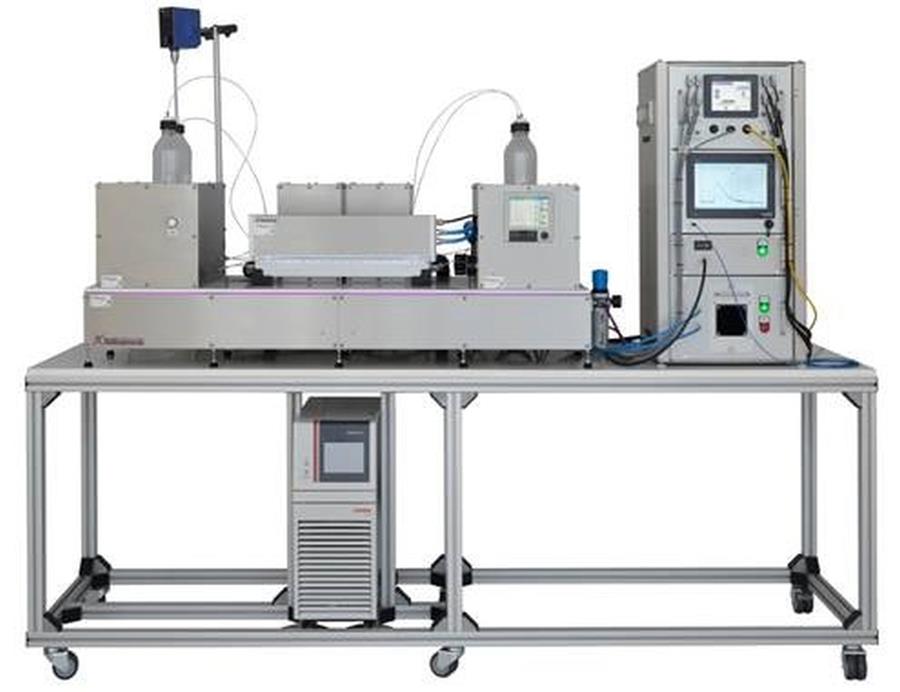
SCALABLE PHOTOCHEMISTRY
As a result of photochemistry's former niche market status, it was confined for a long time to laboratory settings in the research community. The perceived lack of scalability hampered efforts to achieve a large-scale industrial breakthrough in the field of photochemistry. Only a few photoreactors have been operating in an industrial environment up to now. These have been specifically developed for just a handful of processes such as the synthesis of vitamins D3 and A (by BASF and Hoffmann-LaRoche), rose oxide (Symrise), caprolactam (Toray) and artemisinin (Sanofi and Huvepharma)."
Photochemistry does, however, have a lot to offer the pharmaceutical and chemical industries. "Working with light is a highly specific way of developing new molecules, and is completely different from thermal activation in terms of activation technology", explains Van Aken. "Light can be used to selectively trigger a specific functional group using a minimum amount of energy."

NEW SYNTHETIC ROUTES
The microflow reactor is a promising concept for continuous fine chemical and pharmaceutical production. The inclusion of photochemistry opens up new synthetic routes, especially for temperature-sensitive components and reactions, where an unwelcome parallel reaction occurs at higher temperatures. Hannes Gemoets, Head of R&D at Creaflow: "The higher degree of selectivity at lower temperatures for well-known transformations is indeed an advantage, but the main benefit is photochemistry being able to access a number of transformations that are not feasible with thermal processes. This allows alternative and shorter routes to a final molecule to be developed using a photochemical process."
Creaflow's reactor development programme was designed to extend the limits of what existing photochemical microreactors can achieve in terms of scale-up.
"A process engineer will ultimately choose a continuous process with maximum controllable energy and mass transfer and minimum residence time distribution, which is also suitable for upscaling with minimum process optimisation. This combination of factors is what makes our reactors stand out from the competition," Gemoets explains.
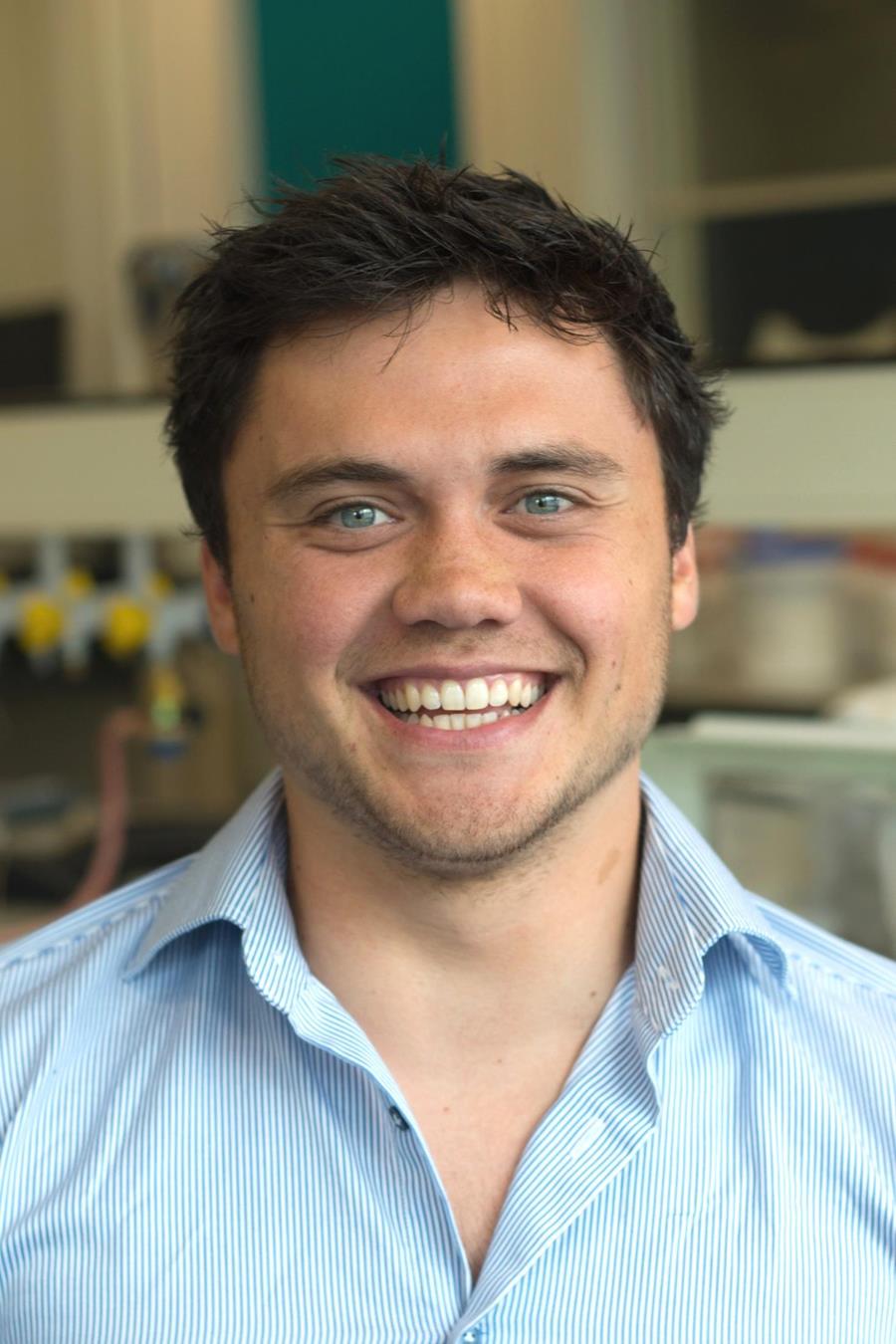
Who is Dr. Hannes Gemoets?
Hannes P. L. Gemoets was born in Ghent (°1991). In 2013, he obtained an M. Sc. Degree in Chemical Engineering (cum laude) from the Catholic University of Leuven (Faculty of Engineering Sciences Ghent). Later that year, he moved to The Netherlands to complete his doctoral studies at Eindhoven University of Technology (TU/e) in the Microflow Chemistry & Process Technology Group, under the supervision of Prof. Timothy Noël and Prof. Volker Hessel. His research focused on the development of new continuous flow methods for C-H functionalisation strategies (i.e. C-H activation and photoredox catalysis). He joined Creaflow in 2018, where as Head of R&D he focuses on the design and development of innovative and scalable continuous flow (photo) reactors.
UNIQUE REACTOR TECHNOLOGY
The unique characteristics of HANUTM flow reactors are achieved by applying the patented COSTATM technology. COSTA stands for:
- Continuous processing in a linear plate flow reactor
- Oscillatory flow regime
- STAtic mixing elements located in the process channel.
PROCESS STREAM PULSATION
Hannes Gemoets explains: "In addition to the normal process flow provided by a pump, a pulsation is applied to the process stream by means of a pulsator that is connected in series, and its combination with static mixing elements in the reactor channel results in a very intense mixing.
One of the unique advantages of this type of operation is that the mixing intensity can be controlled (by changing pulsation amplitude and frequency) and is not influenced by the process flow rate. This is a real game changer for flow reactors, as extremely slow photochemical reactions (requiring long exposure times) can be carried out as part of a fully continuous process, without compromising the mixing efficiency required. Pulsation also ensures a much-improved plug flow pattern, a key parameter for the flow reactor's performance."
The most important feature may be the way the reactor lends itself to a linear laboratory to pilot or even commercial-level scale up by widening the process channel, but without the need to change any process conditions.
“The most important feature may be the way the reactor lends itself to scale-up without the need to change any process conditions”
TEMPERATURE MANAGEMENT
Specially developed in cooperation with our German partner Peschl Ultraviolet (Mainz), high-power LEDs were incorporated into the reactor. The HANUTM flow reactor is designed for both visible and UV light, as it can accommodate both a borosilicate and a quartz window. "LEDs not only enable efficient energy conversion from electricity, but also, thanks to their monochromatic light, no longer generate unnecessary wavelengths that can trigger side reactions or are converted to heat.
The heat is also dissipated very effectively by means of an internal fluid-based heat exchanger located in the close vicinity of the metal process channel."
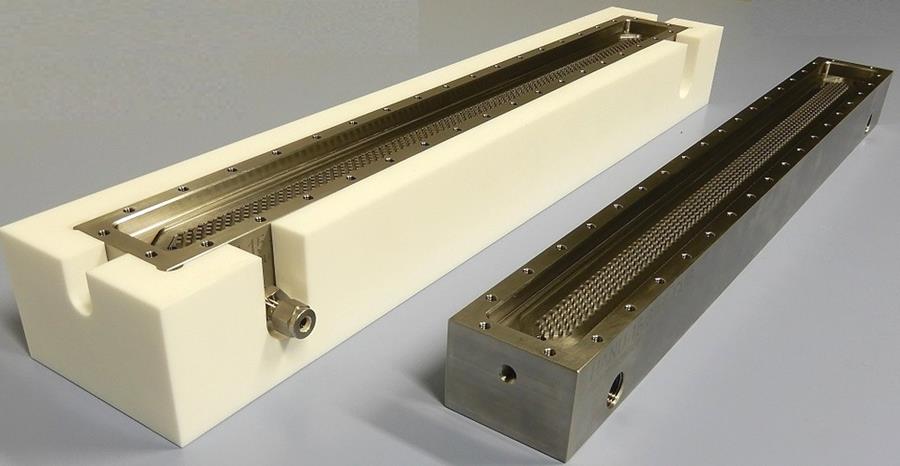
SLURRY PROCESS COMPATIBILITY
The use of solid particles in a process (at start-up or formed during the reaction) is currently a major disadvantage for flow reactors as these particles can attach themselves to the reactor channels and ultimately cause blockages. "The pulsating flow keeps the particles in suspension and allows them to pass smoothly through the HANUTM flow reactor. Our flow reactors can therefore also be used for multi-phase processes such as slurries," says Gemoets.
The window also allows the entire process channel to be visually inspected
“The window also allows the entire process channel to be visually inspected. What's more, our reactor - unlike chip or capillary reactors - can be dismantled to enable the physical removal of any residues that may have attached themselves to the wall of the reactor. This is a key consideration for pharmaceutical applications, where cleaning validation through reactor wall sampling is highly important."
A good example of this is the successful translation of a solid-liquid photoredox-catalysed process from a millilitre laboratory scale to a scalable continuous process. This led to a publication in the scientific journal “Organic Process Research & Development”. High-profile flow chemistry academic groups, including Prof. Timothy Noël (University of Amsterdam, The Netherlands) and Prof. C. Oliver Kappe (University of Graz, Austria), have also recently published scalable processes using HANUTM flow reactors.
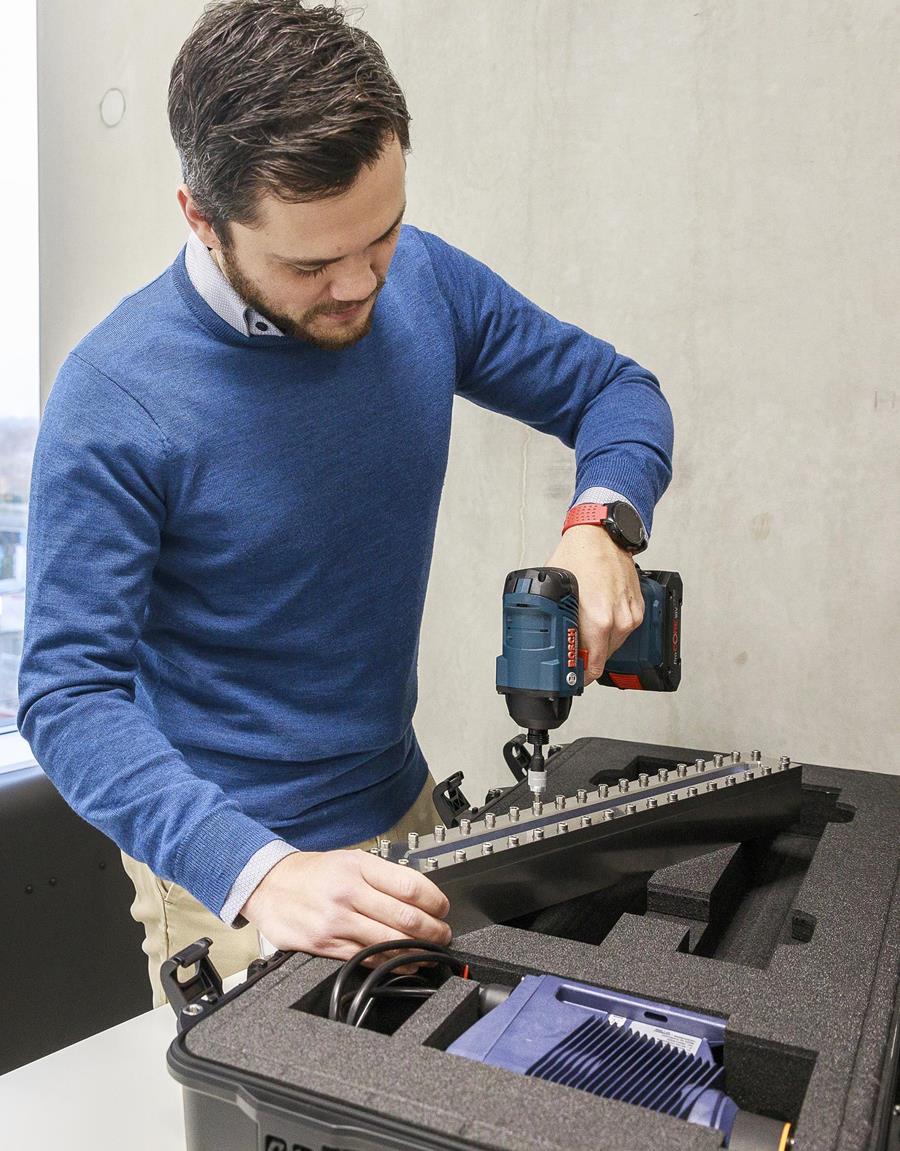
CUSTOMISED assembly
The fact that HANUTM flow reactors can be dismantled offers the additional major advantage of being able to assemble the appropriate components according to the process requirements, such as the compatibility of process flow components with the reactor material and the critical process parameters.
"Reactors can therefore be assembled that are ideally suited to specific transformations so that the reactor is adapted to the reaction and not the other way round as is currently often the case. Consequently, our reactors are appropriate for both photochemical and non-photochemical reactions."
PRESSURE RESISTANCE
Although pressures up to 100 bar are easily achieved in tubular microreactors - which is particularly useful in the case of hydrogenation and oxidation - the pressure resistance of HANUTM flow reactors is limited to 10 bar.
"This because the reactor's composition is made up of different parts: a basic block with glass and cover. However, since more than 90% of all photochemical applications are subject to these process conditions, we do not regard this limited pressure resistance as a constraint," qualifies Gemoets. " Our new reactors being developed for high-temperature (non-)photochemical and high-pressure applications will support process pressures of up to 60 bar."
Who is Dr. Koen Van Aken?
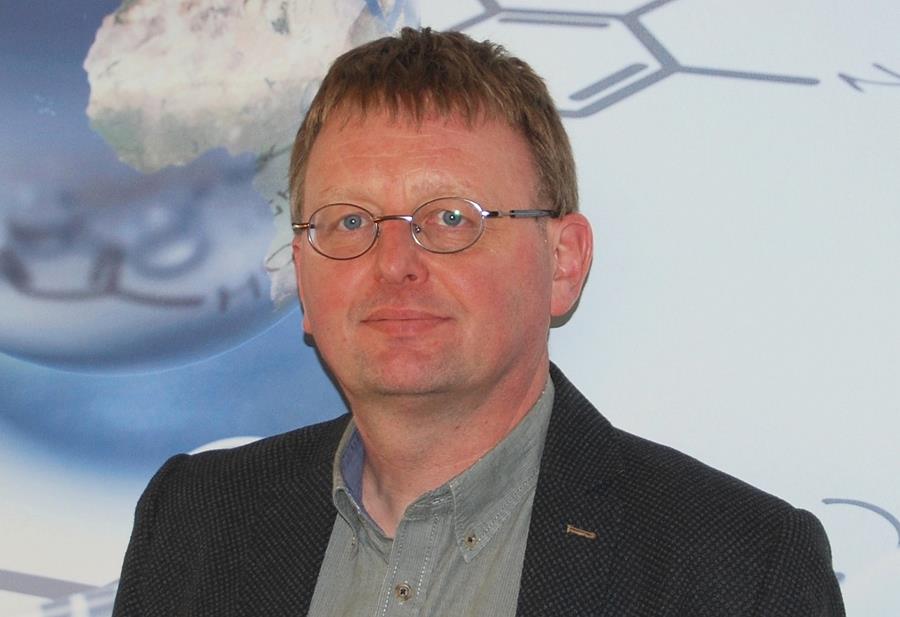
After completing his doctoral studies at KU Leuven in 1993, Koen Van Aken (°1965) held a postdoctoral position at Georgia State University in Atlanta. He then joined the Centre of Molecular Design at Janssen Pharmaceutica (a division of Johnson & Johnson). As a senior scientist, he worked on the design of HIV drugs in close collaboration with Dr. Paul Janssen, which ultimately resulted in FDA-approved drugs. After setting up the company Ecosynth in 2001, he completed a masters’ degree in Innovation & Entrepreneurship at Vlerick Managament School – Ghent (2007). His 23 years of experience in academic and industrial organic chemistry are demonstrated by the (co-)authorship of more than 40 publications (including 17 patents). His main interests are sustainable chemistry, flow chemistry, novel activation technologies, optimisation of reaction parameters, organic chemistry automation and process development. As current guest Professor, he teaches ‘Sustainable Chemisty’ as a course at the Catholic University of Leuven. He also chaired the feasibility study for the Flemish Initiative for Sustainable Chemistry and was a member of the former board of directors of FISCH, now transformed into CATALISTI.
HUGE POTENTIAL
At a time when the 'Internet of Things' (IoT) offers unprecedented opportunities thanks to advanced equipment connectivity, flow chemistry is also presented with a wealth of opportunities. The acquisition of big data combined with technological developments, such as information feedback, model predictive control (AI) and robotisation, are set to revolutionise the way chemical processes are designed and optimised. " Consequently, flow reactors and continuous processes are ideally suited for automation and high-speed in-line collection applications. For example, our German partner Peschl Ultraviolet is incorporating our technology into comprehensive turnkey systems, digitising and automating the process via PLC systems, among others, and we are also looking at in-line photo spectrometric analysis," according to Gemoets.
Creaflow started marketing the HANUTM flow reactor in 2019. "Our potential customers are pharmaceutical, chemical, food and biotech companies seeking to produce new molecules or introduce more efficient processes but faced with the limitations of current generation flow reactors. In the bulk chemicals industry, continuous production has been the standard for years, but more recently an ever-growing number of pharmaceutical and fine chemicals companies are also discovering the advantages of flow reactors. In order to cater for this growing demand, Creaflow recently recruited business manager Ruud Merkx, who will continue to develop all the reactor marketing opportunities. We are therefore extremely optimistic about our reactors' further take-up by industry in the future", Van Aken concludes on a positive note.
“BlueChem offers us future scale-up opportunities”
BlueChem opened the doors of its brand-new premises in the Blue Gate carbon-neutral business park, Antwerp, in early May 2020. Belgium's first incubator for sustainable chemistry helps promising start-ups and ambitious high- growth companies scale up their innovation projects in sustainable chemistry and the circular economy to industrial production level. Creaflow was one of the first companies to establish an office there.
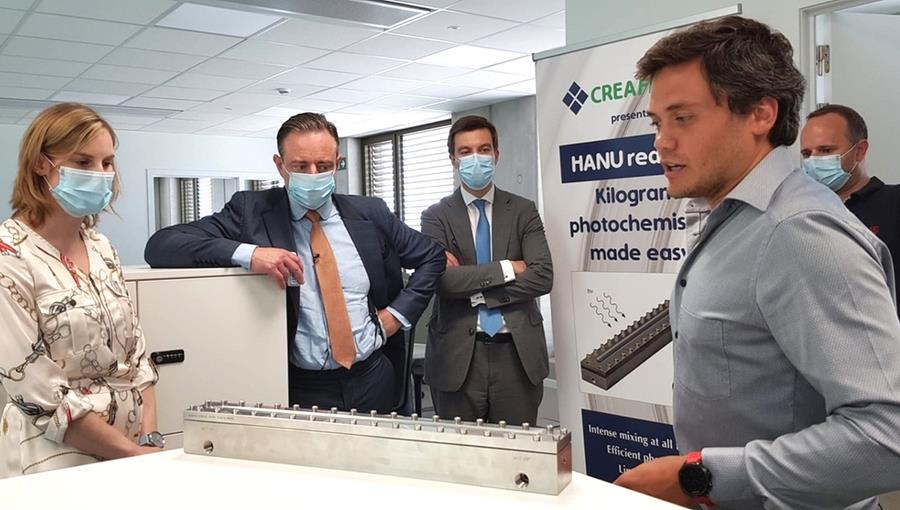
“We are here in the port of Antwerp, at the heart of one of the largest chemical clusters in the world. This base will certainly help us to gain extra visibility," says Koen Van Aken. Hannes Gemoets adds: "BlueChem offers us the opportunity to come into contact with both innovative start-ups and major international players in the field of sustainable chemistry. The cross-fertilisation can lead to further innovative developments and collaborative activities. Thanks to our office at the Blue Gate site, we are not only close to our potential end users, but we also anticipate future scale-up opportunities for Creaflow."
Find out which other innovative start-ups are located at BlueChem.