- 15 januari 2021
- Door Maarten Lubbers et al. (Institute of Biology Leiden, Leiden University)
SuckerSpheres: a sustainable alternative to plastic microbeads
Plastic microbeads are used in a variety of personal care products, ranging from cosmetics to essential healthcare products such as sunscreen. These small plastic spheres, made from crude oil-derived chemicals, are a major source of microplastics. Microplastics pollute the environment and accumulate in wildlife and humans, endangering their health. As the severity of this issue was understood, governments across the world have implemented complete or partial bans of plastic microbeads. Therefore, there is an urgent need to develop microbeads based on sustainable and non-toxic alternatives.
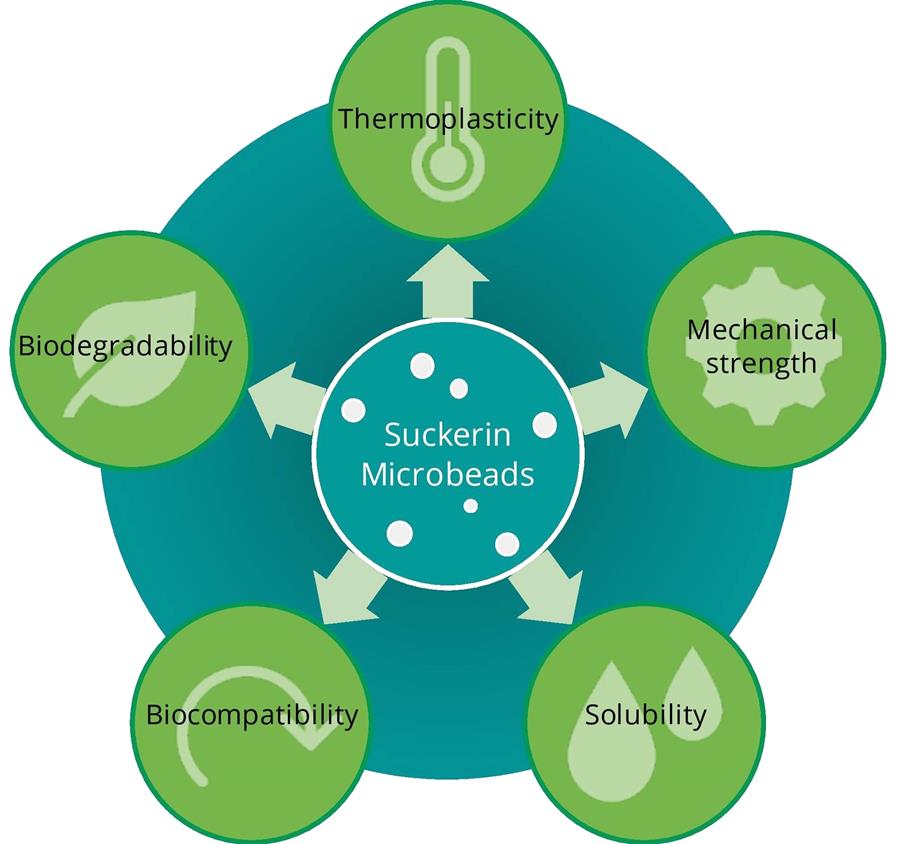
Acknowledgements from the authors
This article was written by Maarten Lubbers, Floor Stel, Jonah Anderson, Daniël Tan, Daan van Tol, Marjolein Crooijmans and Principal Investigators Prof.dr. D. Claessen & Prof.dr. J.H. de Winde (Institute of Biology Leiden, Leiden University). "Our project would have not been as successful as it has become without the help of a number of researchers and stakeholders. We would like to especially thank Professor Peter Punt (Leiden University) and Dr. Kees de Gooijer (Wageningen University & Research) for their valuable feedback during brainstorm sessions."
In recent years, a number of biological materials have gained interest as an alternative for plastic microbeads [1]. Suckerin, a versatile biomaterial found in the Humboldt squid (Dosidicus gigas), gained our attention. In squid, suckerin proteins self-assemble to form sucker ring teeth, toothed rings present on the suction cups of the squid [2]. Suckerin’s flexibility and relative ease of production make it interesting for various applications, one of which being the production of microbeads.
Suckerin: a versatile protein with promising applications
Our team first came across suckerin during a brainstorm session for the iGEM competition. This is a global competition where student teams work on solving societal and scientific challenges using synthetic biology. During the iGEM competition, we developed an application to use suckerin protein in a hydrogel to cure burn wounds. When this iGEM project finished, we dove into other applications of suckerin.
One of the reasons we chose to work with suckerin during our iGEM project, are the incredible properties of the protein (fig. 1). On a molecular level, suckerin has a copolymer-like structure, with rigid β-sheet nanocrystals surrounded by amorphous domains, creating a lattice-like structure. The ratio between these two components affects the mechanical properties of the protein, allowing a wide range of applications.
For instance, suckerin has been used/proposed to be used as a mechanism for drug release with robust mechanical properties [3]. Deepankumar et al. investigated suckerin as an underwater adhesive because of its wet‐resistant adhesion properties [4]. Suckerin has also shown potential as a thermoplastic biological polymer, forming an alternative to petrochemical plastic polymers. The interaction and re-arrangement of β-sheets and the lattice at high temperatures contributes to the thermoplastic properties of suckerin [5]. Indeed, experiments with 3D-printed suckerin have already been reported [6].

After our iGEM project, we entered another competition: The Biobased Innovation Student Challenge Europe (BISC-E) to explore the potential of suckerin as an industrial biobased product.As the BISC-E competition focuses on the field of bio-based products, we were encouraged to make a step towards solving the global microplastic problem. With our project SuckerSpheres, our team aims to first eliminate microplastics from cosmetics and personal care products and provide a sustainable alternative to plastic microbeads in all non-rinse-off cosmetics. Biocompatibility is of utmost importance, especially when the microbeads are used in personal care products and essential healthcare products like sunscreen. Indeed, biocompatibility assays have shown that suckerins are not cytotoxic when tested against various cell lines [7, 8].
Heterologous production of suckerin
To produce suckerin beads in a sustainable and economically viable manner, Escherichia coli is used as the production host. E. coli is an ideal host due to its rapid growth, suitability for batch fermentation processes, and prior success in expressing suckerin genes [9, 10]. More specifically, the BL21 (DE3) E. coli strain is commonly used for protein production in bioreactor settings and allows for efficient creation of a production set-up [11, 12]. To establish a preliminary production process, an existing β-Galactosidase protein production setup has been adapted for suckerin production. Medium is first mixed in a tank and then sterilized. A compressor followed by an air filter provides sterile air to the fermentation. The fermentation proceeds in two steps. First, in the biomass formation stage, E. coli inoculum is grown in a fed-batch culture. Once the cell density is optimal (OD = 1.0), suckerin production is induced through an induction reagent (IPTG). Once the fed-batch is complete, the broth is transferred to a membrane microfiltration unit which harvests the cells from the broth. This reduces the total volume of the fraction containing cells, as well as removing extracellular impurities. Next, the cells are lysed using microfluidization. Cellular debris is removed using a disk-stack centrifuge followed by a dead-end filter. The protein solution is then concentrated using ultrafiltration. Then, the concentrated suckerin solution is transferred to microbead production after passing through a kill tank.
Producing suckerin in a bioreactor set-up provides room for optimization. The medium could be optimized further through chemostat experiments. Furthermore, the carbon element conservation principle can be applied to determine whether substrate degradation occurs. With optimization, it should be possible to increase the production capacity for suckerin from 20 mg/L to 1 g/L [2]. In addition, it is theoretically possible to add molecules to the protein to, for example, improve the anti-age or waterproof properties of the microbeads.
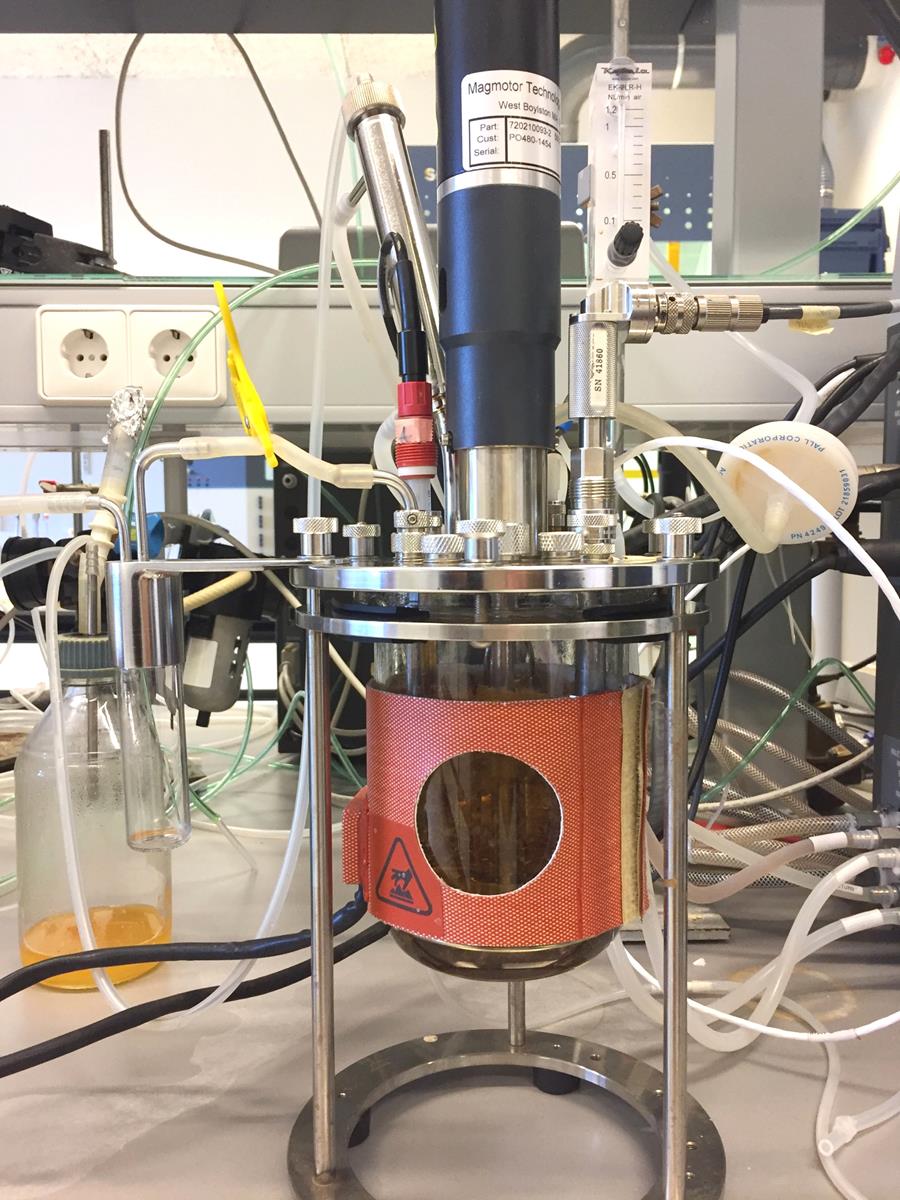
Production of suckerin microspheres
As mentioned before, suckerin has a variety of properties that make the formation of microbeads feasible. Most importantly, at specific pH or salt concentrations suckerin will self-assemble into spheres [13][14]. This eliminates the need for a soluble stabilizer or toxic organic solvent in the reaction mixture, which are currently used for plastic microbead production [15]. More specific methods of microbead production include spray drying or droplet microfluidics.
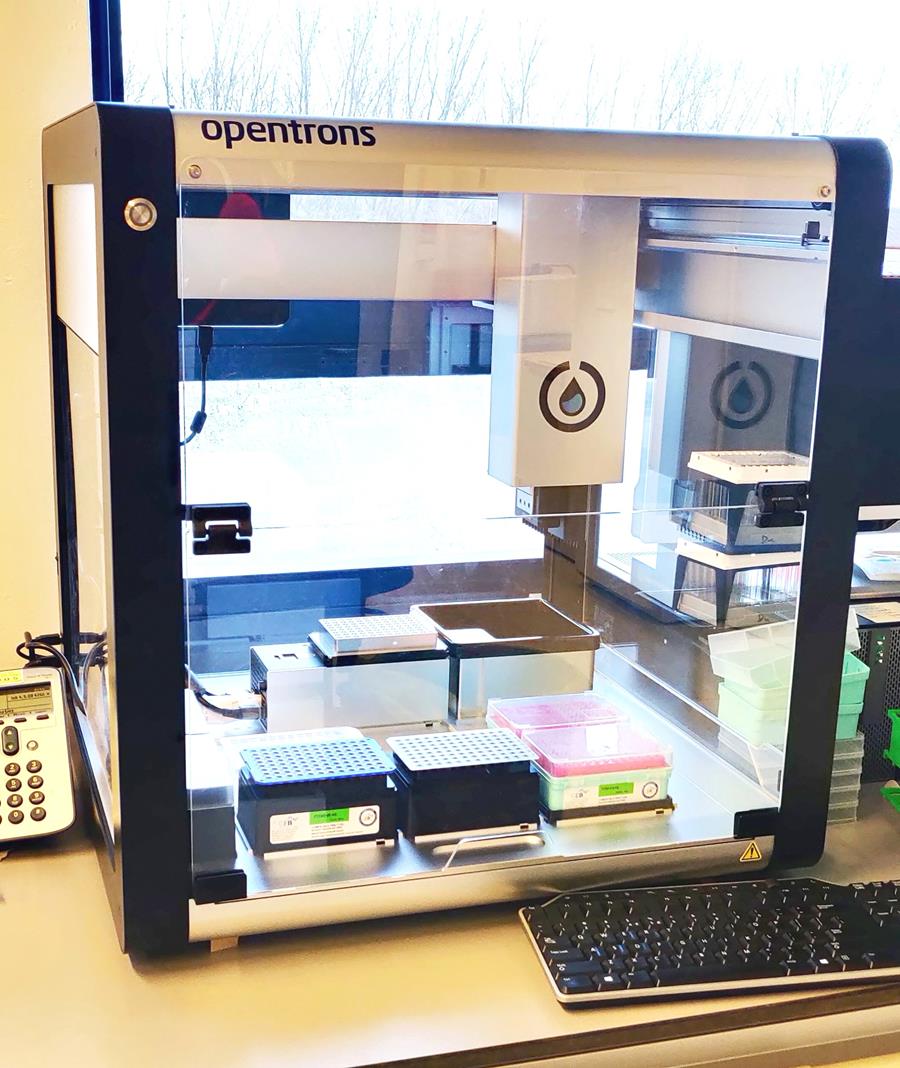
Spray Drying is a common technique to obtain a dry powder of micro-particles at an industrial scale, especially for thermally sensitive materials. It functions by spraying the liquid or slurry from an atomizer, guaranteeing a uniform particle size. Once the fluid droplets are in the air, hot gas is applied to dry the particles. This method can achieve drop sizes from 10 μm to 500 μm [16, 17].
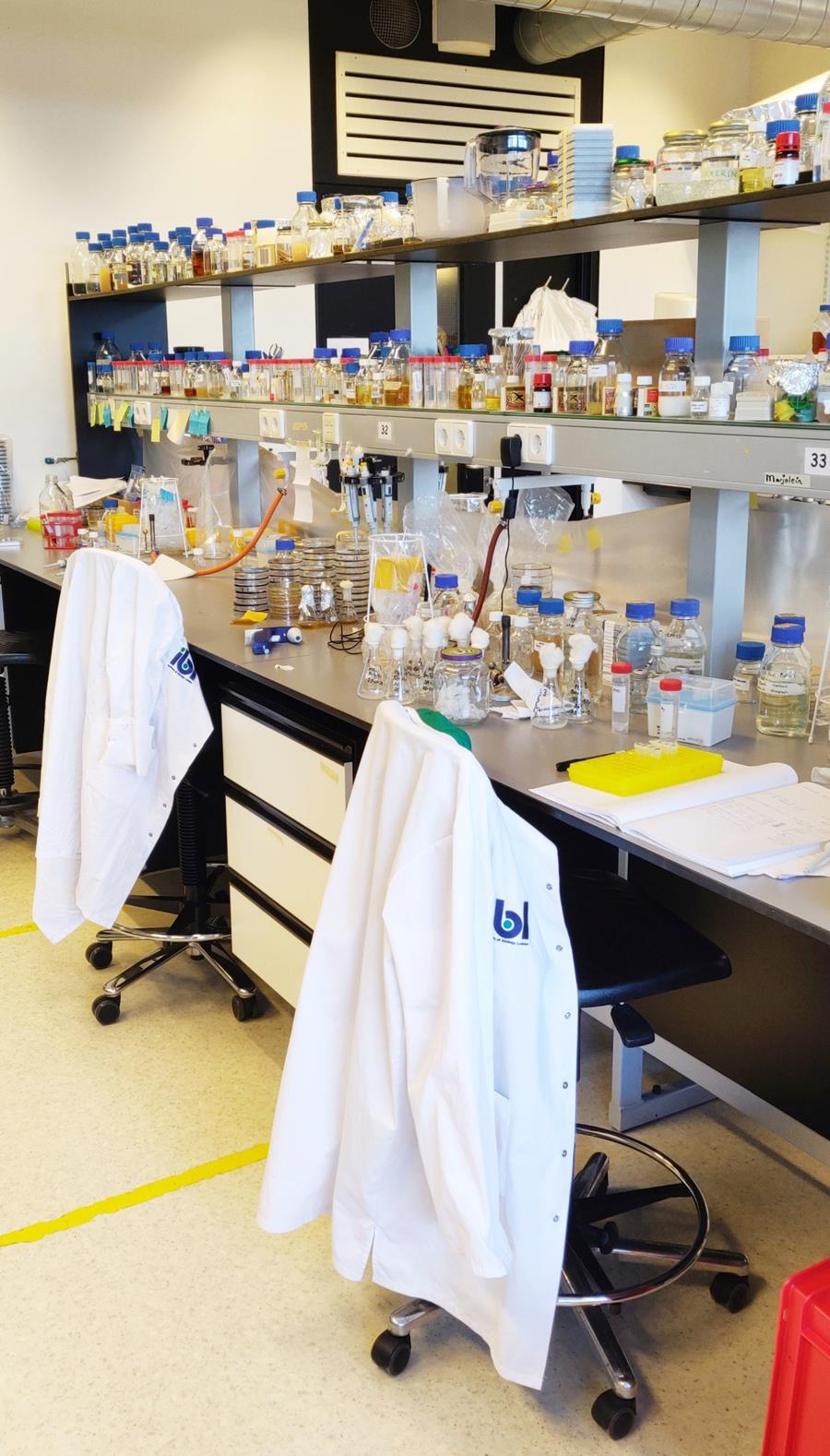
The second technique we tested, Droplet Microfluidics technology, is a recent advance in material fabrication. In this method, droplet production is regulated by the channel geometrics and flow rates of liquids, allowing precise control over the production process. When using these droplets as templates, they can be used to develop reproducible and scalable microparticles with tailored sizes, shapes and morphologies at bulk rates. This technique generally comprises three steps: The formation of micro-droplets by a microfluidics generator, shaping the droplets in micro-channels and lastly solidifying the droplets to form the microbeads [18-20].
Compared to microplastics, the main advantage of suckerin is the fact that it is a protein
The innovation of suckerin microbeads
To investigate the sustainability of our production process, our team looked into various aspects. First, we looked into degradation of suckerin within the environment. Compared to microplastics, the main advantage of suckerin is the fact that it is a protein. We can assume this protein will degrade in the environment without accumulating. In the environment, enzymes will break down all types of proteins into smaller peptides or amino acids, which are then taken up by organisms. Microplastics on the other hand, are barely degraded resulting in accumulation in the environment and wildlife. One other improvement of our product compared with current microplastics is the production process. Non bio-based plastic production currently uses crude oil. It takes a large amount of energy to collect these materials from the natural environment. In contrast, the resources for suckerin production are renewable and environmentally friendly.
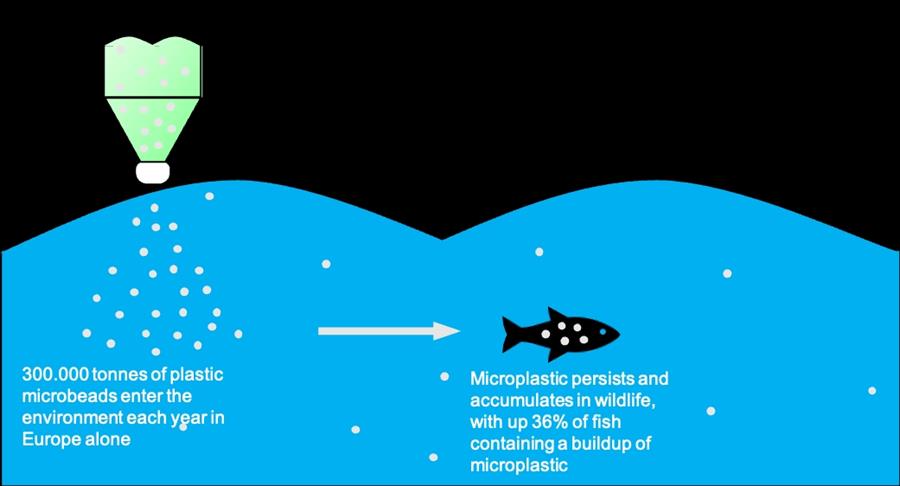
.
To increase process sustainability, second-generation carbon sources from agricultural waste should be included in the E. coli feedstock. Second-generation carbon sources do not have a negative societal impact on food production compared to first-generation carbon sources.
The potential of suckerin as a strong, sustainable biomaterial has inspired researchers to delve into the many possible applications the material can be used for. Due to the simplicity of both the production and processing of suckerin, the material is bound to be a viable alternative for existing biomaterials. Its thermal moldability also makes it ideal as a bioplastic, possibly even replacing regular bulk plastics and making many products more sustainable. Current research focusses on determining the ideal conditions for suckerin production and purification, so more and more applications can be tested. If suckerin can be produced on a large scale, it can have a massive impact on the biomaterial industry.
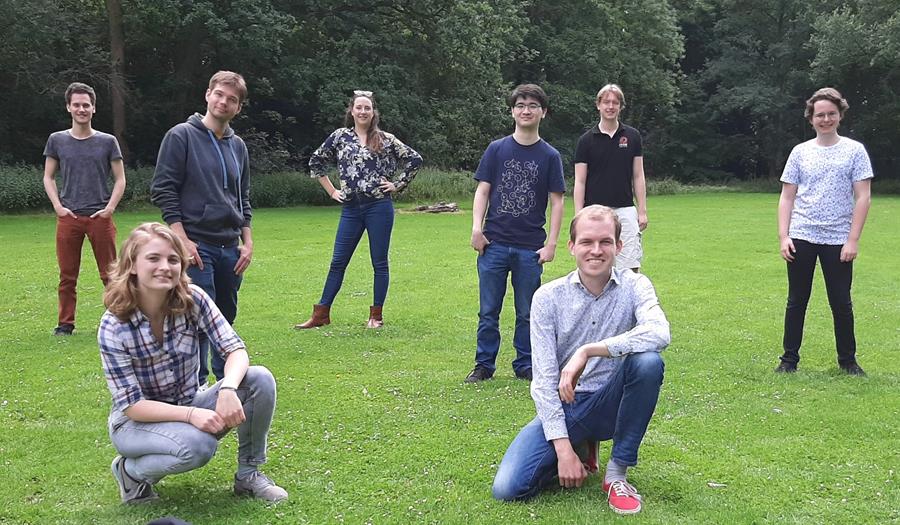
Figure 7: Social-distance group photo of team SuckerSpheres. With from left to right: Laurens ter Haar, Floor Stel, Georgy Bubnenkov, Marjolein Crooijmans, Daniël Tan, Maarten Lubbers (in front), Jonah Anderson and Daan van Tol
Corresponding author: Maarten Lubbers (m.lubbers@umail.leidenuniv.nl)
See the literature list for references